The evolution of the casing scraper
Casing scrapers are not new technology. A quick search on Google patents will bring up hundreds of types of scrapers dating back to the 1930s. In this post we will explore the evolution of this wellbore cleaning tool.
An old technology
Reading some of the old applications gives you an insight into the problems of the day, 80-90 years ago. As long as wellbores have been drilled, there has been a requirement to clean them. We still face many of the same problems today, but fortunately we have become better at solving them.
Old school scrapers are not WBCU tools
The original casing scraper we know today dates back to the 40s. These are what we know today as rig scrapers. There are variants, but typically they are fixed rotating designs with six solid scraping blocks mounted on springs and held together by some rings or bolts.
There is one big misunderstanding about these tools: They were designed to remove large cement deposits left behind by aborted cement jobs and were never designed to be a wellbore clean-up tool. They were just used as wellbore clean-up tools as there was little other choice.
Reinvention in the 1990s
By the 1990’s it was becoming more apparent that the original design of the casing scraper was outdated for the job at hand. It was not uncommon for the scrapers to fall apart during clean-out operations. Also major operators were reporting that the most common cause of Non-Productive Time (NPT) during the completion phase was due to poorly cleaned wells.
This set the tone for a fresh look at not only the casing scraper, but brushes, magnets, circulation tools and a host of other devices. Small companies sprung up in UK and Gulf of Mexico specializing in providing specialist wellbore clean-up tools and services.
As we entered the new millennium wellbore clean-up had moved away from being an after-thought or an unnecessary expense, to being a critical part of the completion operations.
A gold rush among the service companies
Of course it did not take long for before the major service companies to catch on to this. The bold decided to develop their tools in house, while the even bolder decided to acquire. Development of new tools continued funded by growth and speculative investment. Suddenly anyone and everyone (myself included of course!) had wellbore clean-up tools. We have seen some of these come and go so here are my thoughts on the good, the bad and the ugly!
Three lessons learned
In one of my previous blog posts I wrote about The 3 Rs of Wellbore Clean-Up. They are Rotation, Reciprocation and ciRculation. But how do you incorporate this into a casing scraper?
- Rotation – you need to rotate at high speeds for long periods of time without damaging the casing, whether this is to assist with hole cleaning or when drilling cement
- Reciprocation – scrapers of course work by reciprocation, so we reciprocate the pipe up and down to remove cement from critical areas
- ciRculation – insufficient consideration into the flow of fluids through and around the tool is probably the most overlooked basic concept I have seen. Either the internal diameters or the external cross sectional flow area are too small, causing a flow restriction. Not only that, but the maximum object size which can pass around or through the tool has to be considered. You need to have good flow areas and clearly defined flow paths to circulate the debris out of the well and prevent blockages or pack-off
What else have we learned about scraper design?
Firstly – experience proved that fixed block/blade type scrapers were not as effective as flexible scraper elements in cleaning the casing. The reason is that they cannot flex or deform to fit the variances in the internal diameter of the casing that they’re cleaning. Block scraper cause an effect know as “tram lining”. Avoid them at all cost.
Secondly, we had seen the evidence of the superiority of non-rotating over rotating design. But what does non-rotating mean? It means that when the tool mandrel rotates, the centralizers and scraping elements do not. This prevents casing wear and allows high speed rotation up to and above 120 RPM to help clean the well far more efficiently.
Thirdly, single piece mandrels are a subject close to my heart, and I will go to extraordinary lengths to avoid internal connections in a design. Why include an internal connection if you do not need one? The scraper is the most abused of all wellbore clean-up tools and needs to be robust and one of the simplest ways to eliminate internal connections from the design.
The ugly tooth…
Finally, the key function of a casing scraper is to scrape and remove cement effectively and efficiently, and one the best ways to achieve that is BIG UGLY TEETH. Picture Steve Buscemi, Ken Dodd or Janet Street Porter trying to bite into an apple and you will be close to perfection for casing scrapers.
I hope today I have entertained and informed enough that you want to learn more. So here’s a challenge: This link will take you to Google Patents where you will find a casing scraper from 1949. The person who finds the earliest embodiment of a rig type casing scraper (must be deployed on drill pipe only) and posts the link below will get a goody bag with some OWS promotional items. The rest of you can google Steve Buscemi, Ken Dodd or Janet Street Porter to find out what I am talking about.
Topics: Wellbore CleanUp
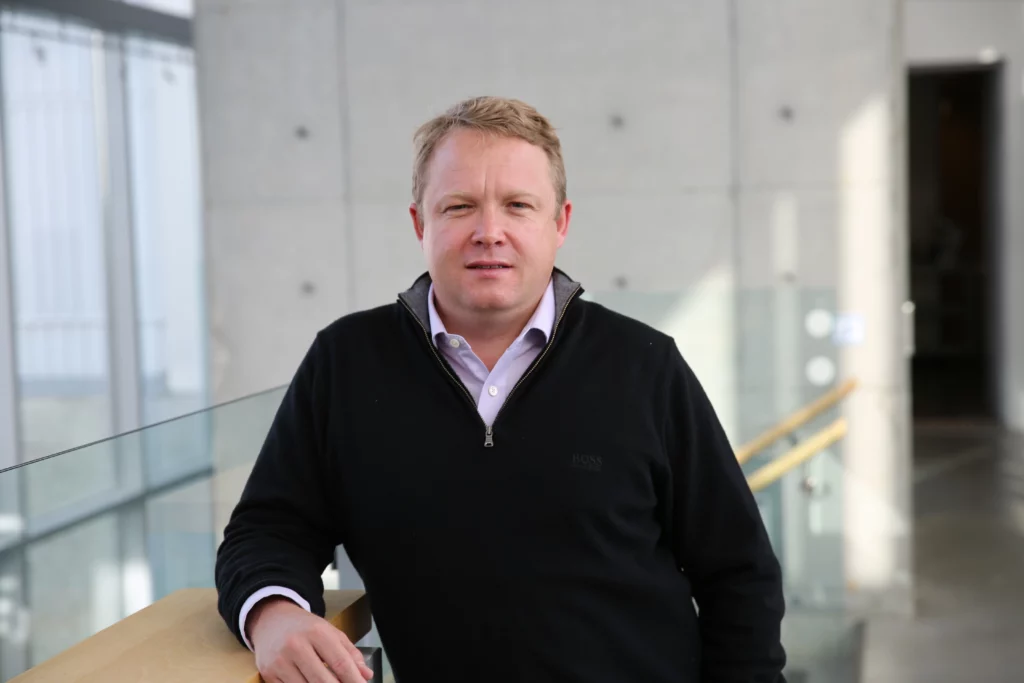
By: Simon Leiper
Simon Leiper has worked in the wellbore clean-up industry for 15 years. He leads the wellbore cleaning product line with Odfjell Well Services and is the inventor of multiple Odfjell patent applications. He has an HND in Mechanical Engineering and has worked and lived in international locations.