How CRTi and Ream Shoe can Reduce Casing Running Time and Costs
The risk of stopping casing jobs before reaching TD is greater for deep and/or deviated sections. The ability to ream casing down by using the CRTi (or CRTe)and a ream shoe overcomes challenging wellbore obstructions such as tight spots, ledges, high dog legs, cutting ‘beds’ or difficult deviated zones.
There are situations where Level 1 casing reaming could save up to 50 percent of the time or more.
In the BHA
Reamer shoe
To be able to ream casing down, you must plan to use a proper reamer shoe. Fixed on Casing or Liner strings, it is designed according to your application needs, and to minimize ECD and maximize Flow-By.
The reamer shoe has a cutting/reaming structure that re-establishes the hole size. The dynamically directed flow ports overcome difficulties when running casing and ensure effective hole cleaning.
Being easy to drill through, and part of your shoe track, the reamer shoe is mostly equipped with high strength profiled alloy front (“the nose”) drillable with standard PDC or Rollercone bits. The exact nature of the well section determines which style of shoe is most appropriate, and similarly, the choice of cutting structure depends on the type of obstructions likely to be encountered.
Some reamer shoes are able to cut and drill thru formations as well (HD versions), so running parameters and aggressiveness of the ream shoe should be proper planned and optimized.
Example of reamer shoe: Pen-O-Trator (DHP)
Centralizers
Depending on well sections and applications, you need to plan the most suitable centralizers for your reaming job.
A casing centralizer well secured around the joint will keep the casing from contacting the wellbore walls and prevent differential sticking. Casing centralization is also one of the key elements in generating a quality cementing job by preventing poor areal isolation.
Term of standoff is related to casing centralization and represents the extent to which the casing string is centered. When the casing is perfectly centered in the wellbore, the standoff is 100%. 0% standoff means your casing touches the wellbore. The goal is always to provide a positive standoff with a maximum torque&drag reduction and maximum flow-by.
On the surface
The most important equipment on the surface is, without any doubt, the OWS CRTi/e tools designed for casing running, reaming or drilling with top drive equipped rigs. It enables connection make up, break out, circulation and rotation and assists in getting your casing to TD the first time, reducing non-productive time and associated costs.

OWS TDCRTi
> Read also:Top Drive Casing Running – Why Would You Look for Anything Else?
Casing Connections
Casing reaming needs to be taken into consideration in the planning phase of the project. Through torque and drag analysis in the planning stage, well engineers have to assess if the casing connection is able to withstand the combined mechanical stresses induced by reaming down the casing.
If heavy reaming is expected, fatigue analysis of the connection will have to be performed using fatigue performance data from the casing supplier.
API casing connections are limited when casing reaming is required, and most of the applications will probably require premium connections.
> Read also: The Difference Between Standard and High Torque Connections
Cut casing running costs
For low to high angled sections, when reaming is expected, a CRTi system and a Ream Shoe is highly recommended to be in place. The extra costs of the ‘reaming equipment’ is low compared to the risk (real costs…) of not reaching planned TD or jeopardizing the integrity of your wellbore.
A fresh example from an onshore rig in South-Eastern Europe illustrates the economical aspects:
With a rig cost at 1500 €/hour, the client was trying to reach TD conventionally for many hours without succeeding. The operator washed down casing (‘reaming’ with a standard float shoe…) for more than 26 hours, and the shoe was finally set 30 meters higher than planned final TD.
On the next well in the same cluster, with similar section TD and geological setup, the operator spent 6000€ extra on a ream shoe, and accessed OWS CRTi system.
This simple solution brought them savings of more than 30k€, and section was “closed” at the planned TD, followed by a successful cementing job.
Topics: Casing Running
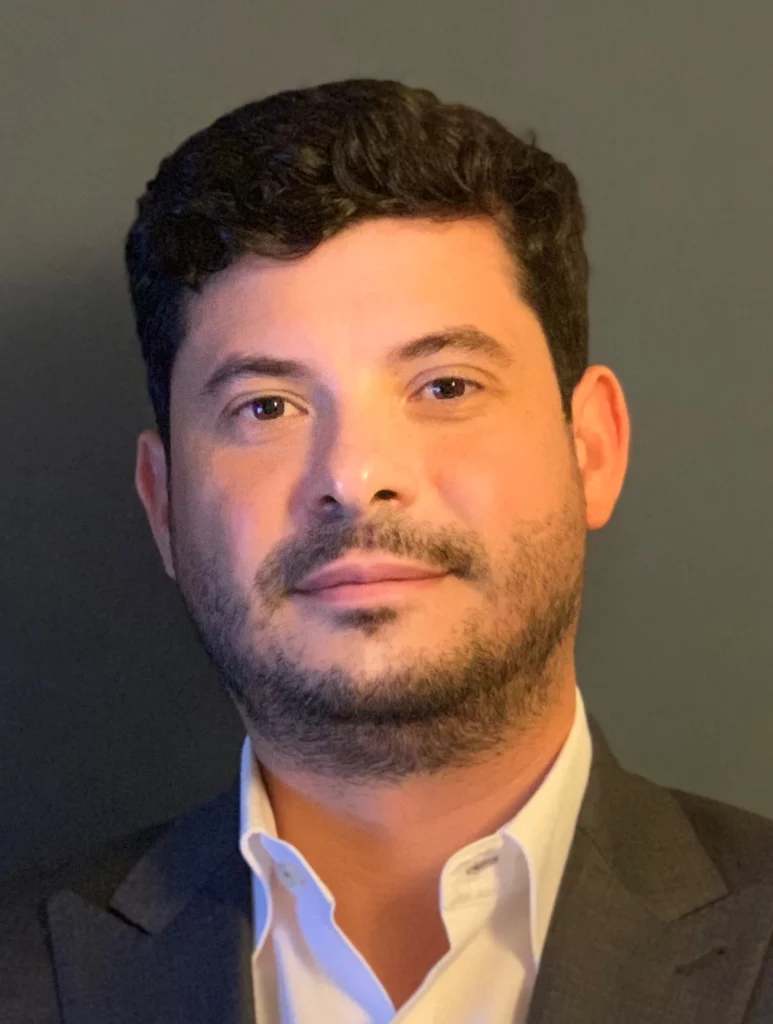
By: Alexandru Gomoescu
Alexandru has been in the oil and gas industry for ten years providing drilling related services such as casing drilling, tubular running and drilling equipment rental. He is now Regional Manager (CESEE) at Odfjell Well Services.