How offshore experience prevents us from making the same mistake twice
Mistakes cost time, they cost money, they can put a stop to operations, cause material damage and uncontrolled discharges to the environment. Worst of all, mistakes can result in safety failures, injuries and even fatalities. In this post we’ll cover a few ways our offshore experience has helped us and could help you avoid making the same mistake twice.
For all of us, our main goal is to avoid making mistakes, unfortunately we’re only human and, at some point, they’re bound to happen. Even with a highly experienced rigsite crew, mistakes happen. The important thing is to learn from our mishaps and implement actions to bypass these blunders.
How can we prevent mistakes from recurring?
1. Understand what went wrong
OK, time to get your magnifying glass out and put your deerstalker hat on, Sherlock.
It’s vital to know exactly what went wrong to avoid the same scenario happening again. Thorough examination and inspection of “the crime scene” must be undertaken by trained investigators in order to collect all the facts about why and how the situation occurred in the first place.
2. Documenting and disclosing
Once these detectives have identified the direct and root causes, it’s critical the information gets documented to a high standard and that actions are immediately put in place to avoid repetition. It’s important to create a proactive, quality driven culture through transfer of experience. If there is a safety issue with the equipment or methods/routines, a bulletin must go out to inform the rest of the industry about any dangers that have transpired. If no one knows the procedures to prevent mistakes, mistakes will happen again. To be able to learn from other’s mistakes in the industry, we need to create a safety information system that collects, analyses and disseminates information from incidents and near misses, as well as from best practices. If those who manage and operate the system have current knowledge about human, technical, organizational and environmental factors that determine the safety of the system as a whole, then you have an informed culture. An informed culture is a safety culture.
3. Improving our equipment
Very often modifications to equipment must be executed, or at least approved by the manufacturer. It is common practice for companies to work together with manufacturers to find the best and safest solution to improve the equipment.
When manufacturers issue product bulletins, including Safety Alerts, Product Information and Technical Information, it is important to have dedicated personnel in the organization who are responsible for notifying all relevant parties.
Technical safety alerts/recommended equipment modifications affecting the company’s equipment pool must be implemented through maintenance instructions, and modifications must be executed, logged in systems and communicated to all relevant staff onshore and on rig site.
It’s beneficial to ask the employees who have expertise, to give input on the equipment and how it can be improved to make it safer and more efficient and avoid recurring incidents. When the users are involved in finding solutions, their job satisfaction will increase and they will better adapt to changes.
4. Training
We must utilize learnings from incidents and near-misses to develop best practices, which is a technique or methodology that, through experience and research, has proven to reliably lead to the desired results; avoiding injuries.
Inadequate training is often seen as one of the root cases after incidents. Developing good training programs, and ensuring the training is continuously refreshed is crucial.
It pays to learn from what we do, and develop best practices.
5. Verifications
Verification and validation activities will ensure that effective corrective actions have been implemented to avoid recurrence. Verification is a necessary part of problem solving, and means that you are seeking evidence that the causes of the problem have been removed or reduced.
As we stated, the key to prevent repeated mistakes is to have a fundamental understanding of exactly what happened, What was the root cause? Why and how did this occur?
Once you understand this and all corrective actions are in place and verified, mistakes are avoidable. But it requires a constant high focus from everyone involved.
The author, Steven Denn, wrote “You can never make the same mistake twice because the second time you make it, it’s not a mistake, it’s a choice”
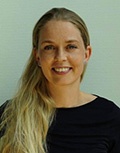
By: Stine Bøen
Stine Bøen has 10 years of experience from the oil and gas industry, working as a quality, health, safety and environmental (QHSE) professional. She is part of the OWS management team in Norway, and among other things, works with QHSE performance monitoring, auditing, managing risk, investigating and following-up incidents and continuous improvement of management systems. Stine has a master degree within Societal Safety.