How to improve casing running efficiency?
The battle against time is a constant challenge for all of us, and it influences all parts of the drilling process. New technology and improvements in methodology alters the way we work, but in my opinion, there are plenty of room for improvement on the processes we have already established. Careful preparation and planning make way for a cost efficient casing running process.
Crew mentality and awareness
The human factor should never be underestimated.
A well prepared, motivated and coherent crew is one of the key factors in establishing and maintaining top performing rig. For a drilling contractor this should be relatively easy but nevertheless a high priority in order to avoid non productive time and maintain a good level of HSE.
For many of the service companies on the other hand, this becomes a gigantic and ever changing jigsaw puzzle, mobilizing and demobilizing a large number of personnel to various rigs. The service company operators may also have a hard time familiarizing with a large number of rigs, drilling companies and operators while at the same time delivering a flawless service to their customers.
So what to do in order to alleviate this vagabond style way of doing things?
Having all service companies on site for the duration of a well is obviously not an option. However, having at least one person on site has a huge impact on planning, coordination and actual job performance. Even though there is a cost associated with this, it is in my opinion, greatly outweighed by the benefits.
Such as:
- Better planning
- Better communication
- Later mobilization of the remainder of the crew
- Earlier check of equipment
- Job ownership and sense of responsibility
Pipe handling
Having a dedicated horizontal to vertical pipe handling system when running casing is highly preferable. Having a dual derrick rig with the capability of racking stands of casing, will also cut the operational time to run a casing string by more than half.
Removal of protectors can also be done more or less effective. When the protectors are removed on pipe deck, time is saved but the risk for damaging the connectors rises. The use of Snap-on protectors will reduce pipe-handling time due to the little effort needed to remove them compared to a regular protector.
Improvement on technical limitations
Every project has its own set of challenges and solutions. The fixed parameters and specs provided from manufacturers take more of a “one size fits all”- form. The ability to evaluate the specs and discuss optimization with the client may result in greater efficiency without sacrificing safety or the careful handling of equipment.
- The acceptance/tolerance for MU of the shoetrack may be revised in close agreement with the client.(My collegue, Robert Koendering, discusses Casing MU Torque and Turn in this article)
- The ballasting of the rig. Level is not always the best condition given a pipe length of several thousand meters. By communicating the best option to the Drilling supervisor, the ballasting may be optimized before or during the casing operation.
- Anti collision system. This software-based surveillance of remotely operated equipment can be too restrictive and may be optimized to increase efficiency.
- Minimize crane activity. Big cranes carrying huge loads make the rig move and that can be critical in certain moments of the casing running process. The operation plan should foresee this and be communicated to the Drilling supervisor.
Casing filling
Casing filling has a great potential for increasing efficiency. If you can implement tools or methods for filling every casing joint as it is run in hole, you can increase the running speed by up to 30% on large OD casings, such as a 20”. Not having to stop and fill the casing every 5 to 10 joints, wil lead to a continuous operation and have a direct impact on running speed. Using an autofill casing shoe is also an option, but they will limit your circulation capability, and may be an issue with regards to both barriers and backflow. Despite the apparent benefits of filling every casing joint, a different set of challenges are introduced, such as added cost, extra rig-up of equipment or big changes of the casing running set-up. But despite the challenges, there is a huge potential for saving time and money.
In this article I talk about the benfits of Top Drive Casing Running
Don’t skip the homework
There is no doubt that the decisions and executions on site are in close relation to the planning of the casing process. The operators on site are the most important factor of course, and the way they conduct themselves executing the tasks is key to efficiency, safety and economy. By planning carefully and communicate openly, we ensure that they have the best possible conditions to deliver at the highest level.
Topics: Casing Running
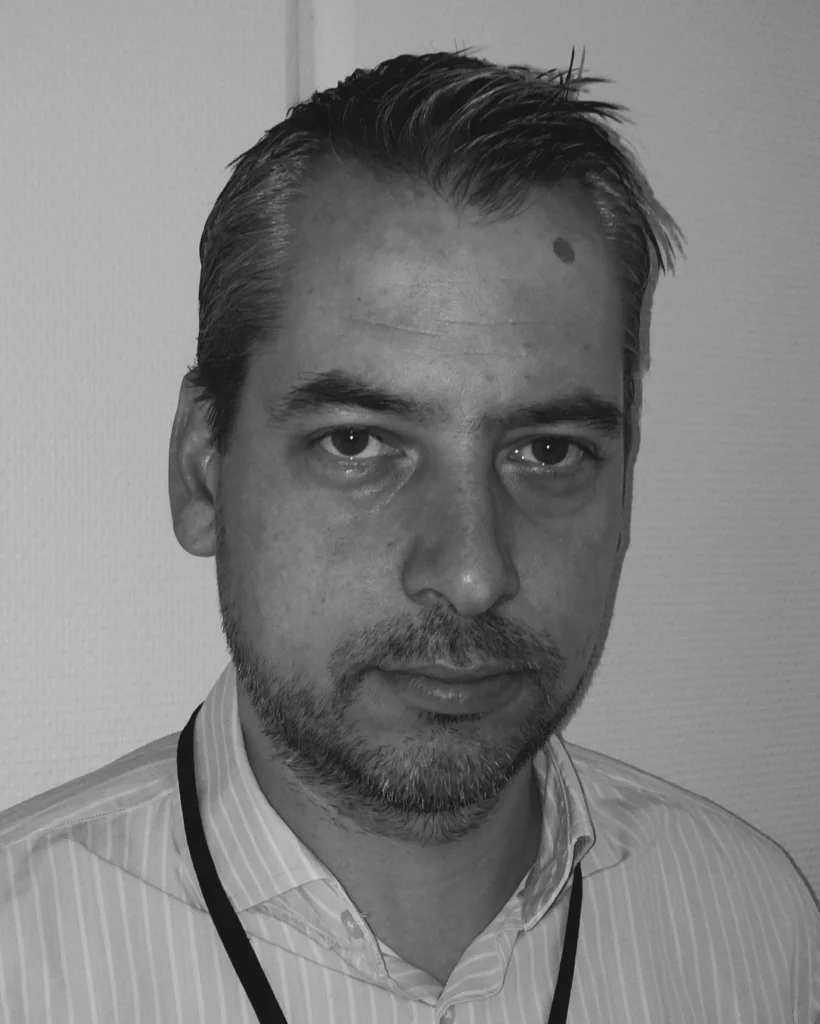
By: Cato Gjesdal
Cato Gjesdal has 10 years’ experience from the oil & gas industry. As Sales & Project Engineer in Odfjell Well Services, he works with clients optimizing and improving tubular running operation such as casing running, P&A, completions and well testing.