Implementing global standards for casing, wbcu and rental
How can we prevent making the same mistakes? How can we ensure that we follow best practices throughout the organization? How can we keep track of people and gear? Also, how can we simplify the invoicing process? At Odfjell Well Services we are currently in the verification phase of a roll-out of global standards connecting all parts of the value stream – including HR, time capturing, logistics, planning, financing, mobilizing, demobilizing and maintenance processes- across all sites and business units. By doing so, we increase both safety and efficiency, positioning ourselves for growth. I will share with you the strategy and the thoughts behind this tough project.
Why global standard?
Odfjell Well Services has emerged from a Norway-based service company to a global player in the oil and gas industry over the last 10 years. We have service units in different locations throughout the world, and this type of growth challenges our IT-systems and the way we work.
The Global Standard project is a tool to increase our predictability. The overall goals are to:
- Reduce risk
- Improve control
- Reduce quality cost
- Prepare OWS for further growth
> Read also : Lean in Well Services offshore and onshore
What’s included in global standard?
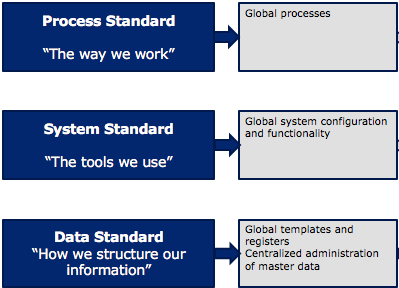
Capturing the way we work
You have to capture an enormous amount of input, and it increases with the complexity of our operations and the number of parties involved. We have arranged our work at OWS in workshops throughout the different competencies and product lines one base at the time. We have gathered the various departments and mapped the processes. The primary goal is, of course, to identify deviations from best practices and local adoptions. However, this work also aims to create efficient workflows that everybody understands and can maintain easily. This is a four steps process.
- Map the way you work
- Map the ideal way to work
- Analyze the gap
- Manage the process to move from 1 to 2
Local deviations
The most common objection against Global Standard is that different local requirements, customs, and products vary, so one size does not fit all. Well, you have to accept that when customer needs vary, equipment and procedures vary. Moreover, when local requirements collide with best practices, you have to come up with a workaround. The point is that you have to be very clear and understand where you enforce a global standard and where you accept local deviations. Standards do vary with geo markets, but we would never compromise on quality, safety, and efficiency, or our core values.
> Read also: The value of 4 decades of offshore experience
The benefits of global standards
Less: | More: |
Time used for error correction | Controlled master data globally |
Manual jobs due to transaction errors | Discipline |
Different work processes in Business units /regions | Standardized ways of working across locations and operations |
Excel sheets | Improved possibilities and functionality for reporting |
Duplication of transactions | Training of new employees + refreshment courses |
Paper, printing | System supported decision process |
Manual work, including data registration | Better system management and support |
Number of systems to executive the same job | Well functioning systems both offshore and onshore |
This is beneficial to both OWS and the clients. Everybody is in line with the customer’s demand from the start of a project. Every document, certificate, specification sheet or contract is located under the same job number. During and after the project, the client’s feedback is now captured and instrumentalized, ensuring even more streamlined and efficient process the next time around.
We believe an integrated system and standardization of work processes and system usage globally will contribute significantly to improving our predictability; delivering the best quality in the most efficient way while eliminating double work, extra work or re-work to our workforce.
Topics: QHSE
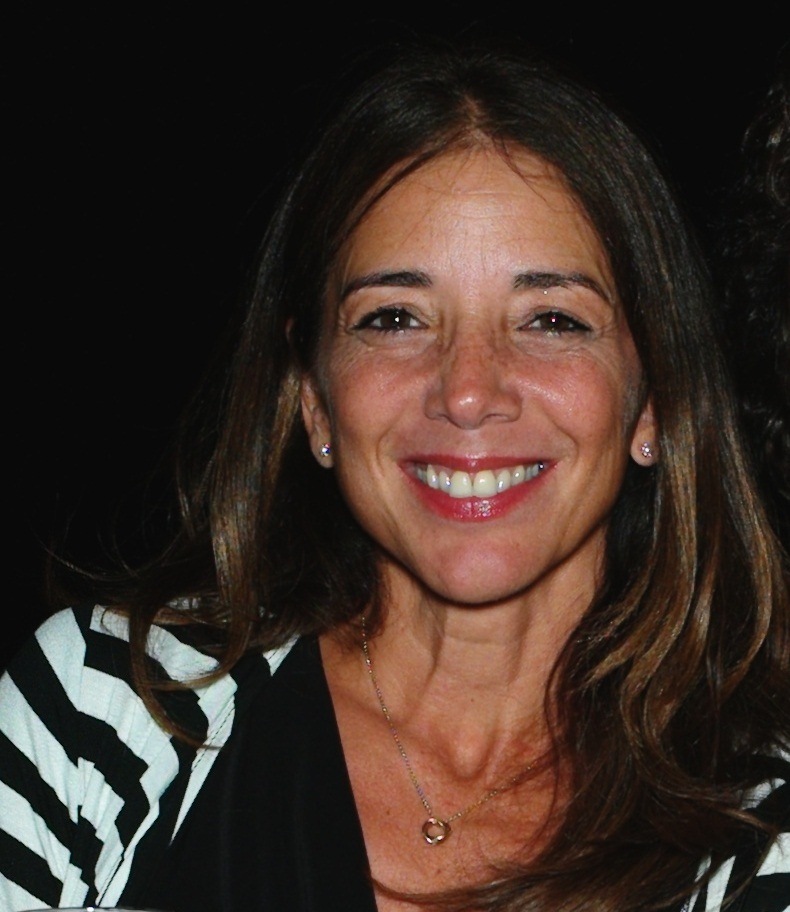
By: Sonia Anderson
Sonia has over 20 years experience (nearly 30) working as a quality, health, safety and environmental (QHSE) professional with a diverse background from international assignments in both private and public sectors. Her early experience was in the US Public Health Service as an engineer officer in different government programs for consumer protection and disease prevention. She spent the last 15 years working in the cruise industry, aviation industry and now recently in the oil and gas industry in different positions within QHSE. Sonia is part of the management team in OWS and as VP QHSE is responsible for leading the OWS global QHSE team and continuously improving QHSE management systems and performance.