Radio operated equipment reduces risk in casing operations
From my location in Thailand it is obvious that a change of culture is taking place. While the remotely operated casing equipment traditionally has had its main market in the North Sea, things are now turning in Asia. The popularity of automated equipment is directly reflected in the reduced number of casualties from production in our region. How do you get the most out of your radio operated casing equipment?
Rig survey is the key point
As always, the benefits of fantastic equipment are limited to the skills of the ones operating them. I cannot stress enough the importance of a solid rig survey for the success of your operation. It only takes a few hours, and without it, you are just guessing. From a rig survey you’ll be able to tell if your equipment fits the rig or if it needs modifications. You will find the proper fittings for the hydraulics and you will talk to the engineers and crews to find the best applications possible.
The rig survey makes you look professional and protects your crew from the humiliation of showing up on the rig with equipment that is not installable.
The scissor table
The scissor table can be looked upon as a framework for different tong sizes from which you can run casing, tubing and drill pipe. Being tied to the rails on the drill floor, the scissor table removes the need for hanging casing tongs, taking away the hazards of dropped objects or being struck or squeezed by tongs in motion.
Since the scissor table’s height is adjustable, you eliminate the need for work platforms, keeping your crew on the drill floor.
> Read also: How to manage risks and hazards in casing operations?
Excellent communication with the driller
The operation of the scissor table is done from a belly pod, and the operator may run from the drillers cabin. A huge advantage for the communication between the driller and the tong operator. The security is not compromised given the featured emergency switch on the belly pod, always accessible for the operator.
Crew’s point of view
The hazardous environment of a drill deck puts every operator in a potential danger by just showing up. When the remotely operated equipment removes people from the red zone, a lot of positive outcome is recorded.
- Stabber guide replaces the need for hands on tubulars
- People won’t get spilt on if fluids flows out of the casing
- A hose might burst without people being affected
- A cold cutter is mounted on the scissor table, removing hands from the casing cutter and eliminating possibility for injury
By using radio-operated equipment you potentially reduce a four-man operation to a two-man operation. I was aiming this article on safety, but it is really hard to overlook the economical benefits in using the new technology.
Safe and cost effective
It’s hard to tell which came first, the chicken or the egg. I.e. did the new technology represent a potential for saving lives, or did increased focus on casualties in production result in a demand for remotely operated production equipment. Nevertheless, the equipment is here, it is performing wonderfully and the contribution it makes to increased security for the workers on site is only equalled by its dominant effect on efficiency and cost reduction.
> Read also: 4 ways to avoid having people in red zone
Topics: Casing Running, Casing Preparation
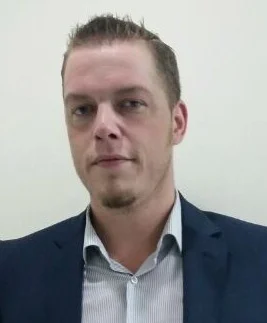
By: Robert Koendering
Robert has 15 years experience in tubular running services which comprises pile driving, running casing & high chrome completions, bucking & pressure testing. He is an expert on top drive casing running tools & DwC operations (Level 2).