The “anatomy” of casing drilling bits (L2)
The idea of using drillable bits on casing strings for CwD applications is a great one as long as you choose the correct bit for your job. These are some of the properties that make a CwD bit different from a conventional drill bit, and a great solution to drill the surface sections, both onshore and offshore.
The bit stays at TD – a non-retrievable product
The material used for a CwD bit has to make room for a compromise; the bit must be “hard” enough to carry high ROPs and many meters, and soft enough to be drilled out easy and quick as a standard shoe.
As you may know by now, a casing drilling bit will remain at the bottom when the planned section reaches its TD. This is a non-retrievable system, and a maximum TD is very dependent on geology; soft formations and shallow sections being the best suitable. The next planned BHA (using standard PDC or roller cone bit) will drill out the casing drilling bit as a standard shoe/shoe track. There is no need for an additional trip, so no time lost due to extra runs.
Metallurgy
In our applications we use premium casing drilling bits, PDC type. The drillable alloyed steel body is machined from a wrought metal bar. With this exception, steel bits are made with the same process as for matrix bits. The steel body is very resistant on impact and less resistant to highly abrasive formations. The cutters are mostly Tungsten Carbide for shallow depths and unconsolidated layers. PDC cutters are chosen for deeper, consolidated or more compacted sections. A mixed cutter structure is also available or possible to customize per client needs.
The bypass port
A very important feature of the CwD bit is the bypass port, also referred to as burst disk. Since the “CwD L2 BHA” is never pulled out, you need to cement through the casing drilling bit and its nozzles. If the nozzles get blocked (before cementing operations or while drilling, for instance when pumping LCM to mitigate losses), the whole section might be in jeopardy. Without the bypass port, you’d have to pull out of the hole and replace the casing drilling bit or continue with conventional drilling. This is where the bypass port comes to rescue. It bursts open to allow cementing operation in the event of plugged nozzles.
Bit sizes
In this article you can see the most used bit sizes for various sections and casings. The small annulus between the OD of the bit and OD of the casing will give you lots of benefits while drilling (“smear effect, high velocity, and good borehole cleaning). This generates high benefits and for the cementing operation: Less cement excess planned, and important cost savings for the client.
Constant development
Like all other areas in the industry, the CwD bits are continuously being improved. We work closely with our supplier and use our experience as inputs to the R&D processes. For the time being (Nov 2015) a new set of CwD bits are up for launch and we expect them to deliver enhanced performances and contribute to even better economic benefits for clients demanding Casing while Drilling.
Topics: Casing drilling
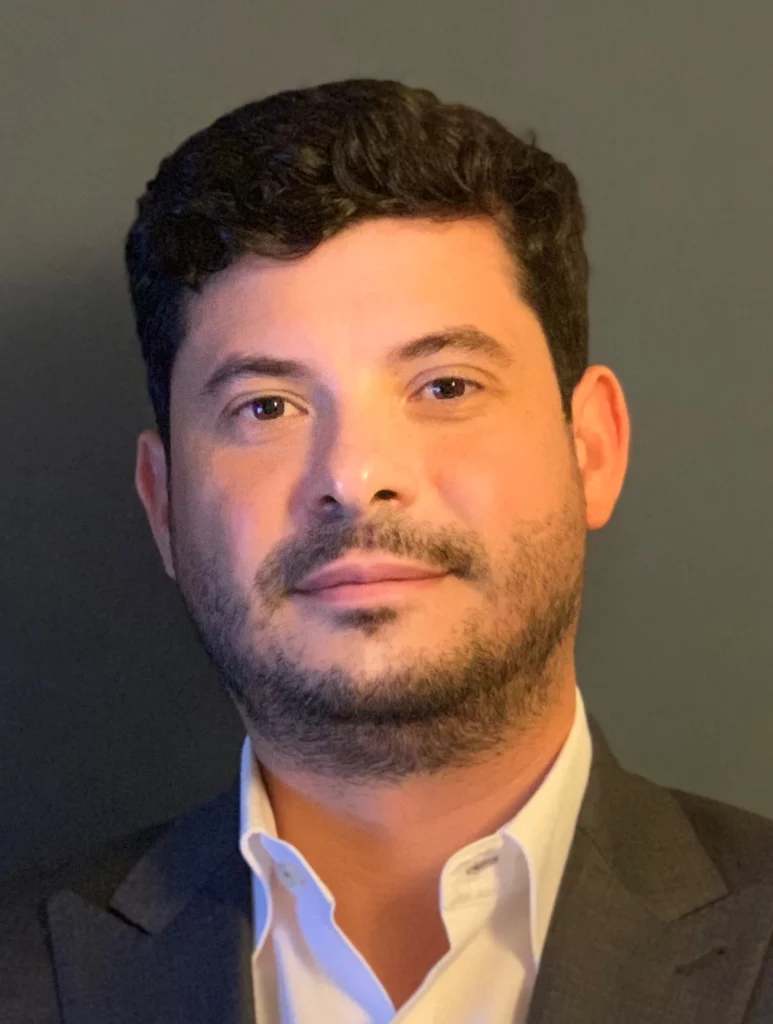
By: Alexandru Gomoescu
Alexandru has been in the oil and gas industry for ten years providing drilling related services such as casing drilling, tubular running and drilling equipment rental. He is now Regional Manager (CESEE) at Odfjell Well Services.